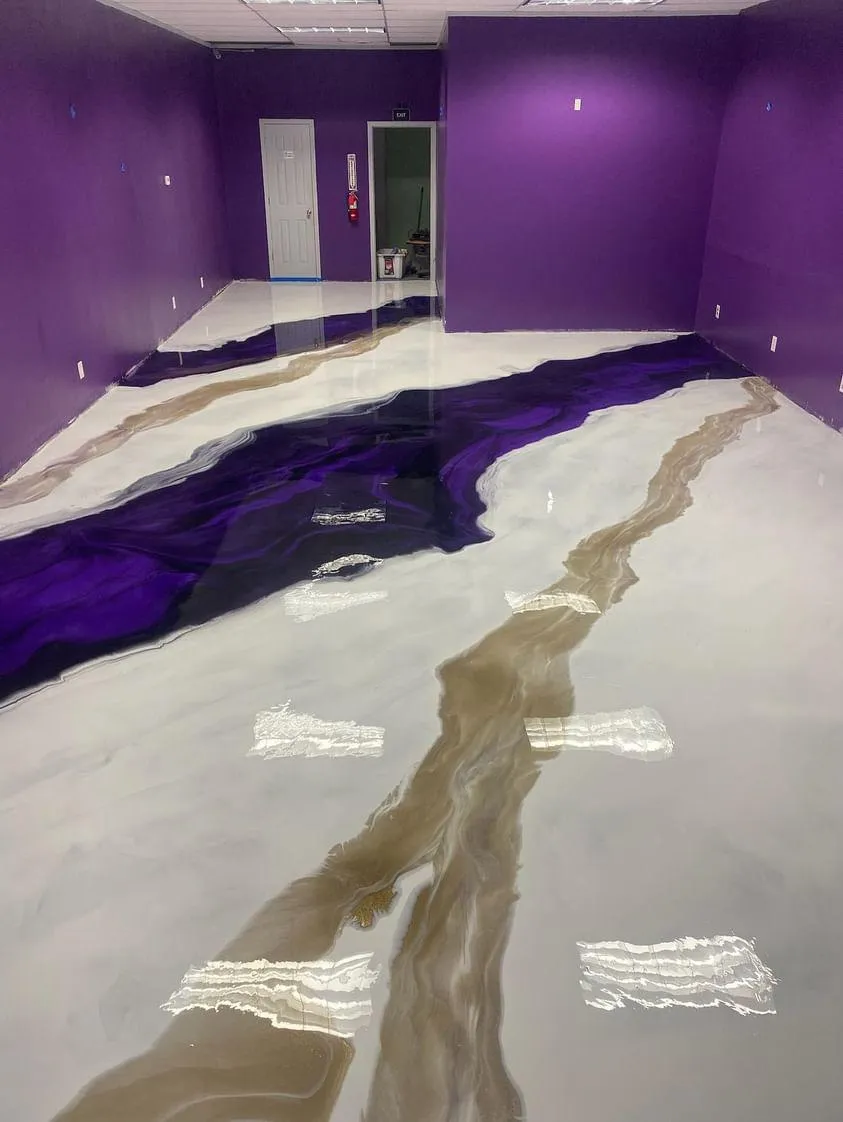
Comprehensive Solutions for Common Epoxy Flooring Problems | Onyx Luxury Epoxy
Epoxy flooring is a popular choice for both residential and commercial spaces due to its durability, aesthetic appeal, and versatility. However, like any flooring solution, epoxy can face certain issues if not installed or maintained properly. At Onyx Luxury Epoxy, we pride ourselves on addressing these challenges head-on with our expertise and high-quality materials. In this blog, we will discuss common epoxy flooring problems and explain how we handle them to ensure our customers receive the best flooring solutions available.
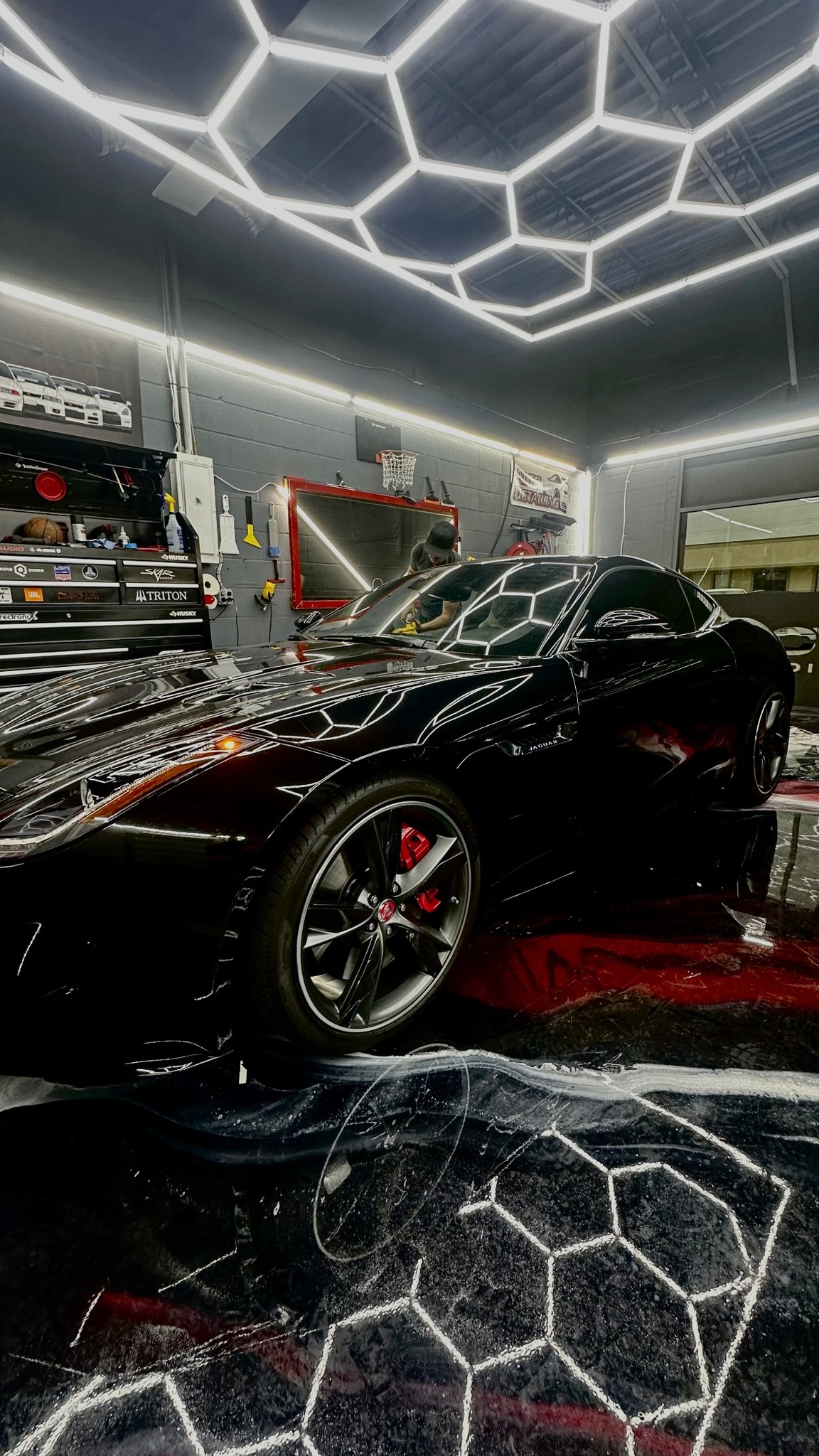
Poor Surface Preparation
One of the most critical steps in the epoxy flooring process is surface preparation. Poor preparation can lead to various issues, including poor adhesion, peeling, and bubbling.
How We Handle It: At Onyx Luxury Epoxy, we ensure thorough surface preparation by cleaning and profiling the concrete substrate. We use industrial-grade grinders and shot blasters to remove any existing coatings, stains, or contaminants. This process creates a rough surface profile that enhances epoxy adhesion. Additionally, we repair any cracks or imperfections in the concrete to create a smooth and even base.
Moisture
Moisture is a common issue that can compromise the integrity of an epoxy floor. It can lead to bubbling, peeling, and poor adhesion if not addressed properly.
How We Handle It: We conduct a comprehensive moisture test before any installation. Using moisture meters and calcium chloride tests, we assess the moisture content in the concrete. If high levels are detected, we apply a moisture barrier or vapor barrier epoxy primer to prevent moisture from seeping through and affecting the epoxy layer.
Bubbling
Bubbling occurs when air or moisture gets trapped beneath the epoxy layer, creating unsightly bubbles on the surface.
How We Handle It: Our team at Onyx Luxury Epoxy ensures proper mixing and application techniques to minimize the risk of bubbling. We meticulously mix the epoxy components to avoid introducing air into the mixture. During application, we use specialized tools like spiked rollers to release any trapped air and ensure a smooth, bubble-free finish.
Primer Issues
A primer is essential for ensuring good adhesion between the concrete and the epoxy layer. Skipping this step or using an incorrect primer can lead to peeling and adhesion problems.
How We Handle It: We always use high-quality, compatible primers for our epoxy installations. Our primers are designed to penetrate the concrete and create a strong bond with the epoxy. This step is crucial for the long-term durability and performance of the epoxy floor.
Epoxy Fades
Exposure to UV light can cause epoxy floors to fade and lose their vibrant color over time.
How We Handle It: To combat UV damage, we use UV-resistant epoxy formulations and apply a UV-stable topcoat. This protective layer shields the epoxy from harmful UV rays, maintaining its color and appearance for years to come. For areas with high sun exposure, we recommend using pigmented epoxies that are specifically designed to withstand UV radiation.
Humidity
High humidity levels can interfere with the curing process of epoxy, leading to improper hardening and a tacky surface.
How We Handle It: We monitor environmental conditions closely during the installation process. If high humidity is a concern, we employ dehumidifiers and climate control systems to maintain optimal conditions for curing. This ensures that the epoxy hardens properly and achieves its full strength and durability.
Peeling
Peeling occurs when the epoxy fails to adhere properly to the substrate, often due to poor surface preparation or moisture issues.
How We Handle It: Our rigorous surface preparation and moisture control measures significantly reduce the risk of peeling. Additionally, we use high-quality epoxy products that are formulated for strong adhesion. Regular inspections during and after application ensure that any potential issues are addressed promptly.
Slippery Surface
Epoxy floors can become slippery when wet, posing a safety hazard.
How We Handle It: We offer various anti-slip solutions to enhance the safety of epoxy floors. This includes adding slip-resistant aggregates like silica sand or aluminum oxide to the topcoat. These additives create a textured surface that provides better traction, reducing the risk of slips and falls.
Poor Flexibility
Epoxy floors can crack if the substrate shifts or moves, as epoxy itself is not very flexible.
How We Handle It: To accommodate slight movements in the substrate, we use flexible epoxy formulations that can withstand minor shifts without cracking. For larger areas, we incorporate expansion joints to allow for thermal expansion and contraction, ensuring the longevity of the floor.
Contaminated Concrete
Contaminants like oil, grease, and chemicals can prevent epoxy from bonding properly with the concrete.
How We Handle It: We use industrial-grade degreasers and cleaners to remove all contaminants from the concrete surface. After cleaning, we conduct a pH test to ensure that the surface is neutral and ready for epoxy application. This thorough cleaning process is essential for achieving a strong bond and a flawless finish.
Temperature Extremes
Extreme temperatures during the application or curing process can affect the performance of epoxy.
How We Handle It: We carefully plan our installations around the weather conditions. During extreme heat or cold, we adjust the epoxy formulations and curing times to ensure optimal results. For indoor installations, we use heaters or air conditioning to maintain a stable temperature environment.
Assuming Epoxy is Just a Paint
Many people mistakenly believe that epoxy is just a type of paint, which can lead to improper application and disappointing results.
How We Handle It: We educate our clients on the differences between epoxy and traditional paints. Epoxy is a two-component system that requires precise mixing and application techniques. Our professional team is trained to handle these complexities, ensuring a high-performance floor that exceeds expectations.
Improper Mixing
Incorrect mixing ratios or inadequate mixing can lead to various issues, including poor curing and reduced durability.
How We Handle It: Our technicians are trained to follow exact mixing procedures, ensuring the correct ratio of resin to hardener. We use high-quality mixing equipment to achieve a uniform blend, which is critical for the epoxy to cure properly and achieve its full strength.
Adhesion Issues
Adhesion problems can occur if the epoxy does not bond well with the substrate, leading to peeling and delamination.
How We Handle It: We conduct adhesion tests before full-scale application to ensure compatibility between the substrate and the epoxy system. This proactive approach allows us to address any potential adhesion issues before they become a problem.
Air Bubbles Beneath the Epoxy
Air bubbles trapped beneath the epoxy layer can weaken the bond and create visible defects.
How We Handle It: We use a combination of vacuum degassing and slow, careful application techniques to minimize the introduction of air into the epoxy. After application, we use spiked rollers to release any remaining air bubbles, ensuring a smooth and strong finish.
Cracking
Cracks can develop in epoxy floors if the substrate moves or if the epoxy is not flexible enough to accommodate minor shifts.
How We Handle It: We use flexible epoxy formulations and incorporate expansion joints in larger installations to prevent cracking. Our thorough surface preparation also includes repairing any existing cracks in the substrate to create a stable base for the epoxy.
Weak Substrate
A weak or damaged substrate can compromise the performance of the epoxy floor.
How We Handle It: Before applying epoxy, we assess the condition of the substrate. Any weak or damaged areas are repaired or reinforced to ensure a solid foundation. This step is crucial for the long-term success of the epoxy flooring system.
Chemical Burns
Exposure to harsh chemicals can damage the epoxy surface, leading to discoloration and degradation.
How We Handle It: We offer chemical-resistant epoxy coatings for environments exposed to harsh chemicals. These specialized formulations provide an extra layer of protection, ensuring the floor remains intact and visually appealing despite chemical exposure.
Conclusion
At Onyx Luxury Epoxy, we take pride in delivering exceptional epoxy flooring solutions that address common problems head-on. Our meticulous approach to surface preparation, moisture control, and material selection ensures that our floors are not only beautiful but also durable and long-lasting. Whether you're looking for residential, commercial, or industrial epoxy flooring in Kansas City and surrounding areas, we have the expertise and experience to meet your needs. Contact us today to learn more about our services and how we can help you achieve the perfect epoxy floor for your space.